How efficiently runs your extrusion line?
3 ways to improve productivity
Overall Equipment Effectiveness (OEE) – an indicator of how productively and efficiently a production line is running – has been the leading performance measure in manufacturing for decades. As Industry 4.0 has taken off, compounders have an array of new tools and techniques that can improve OEE scores of their extrusion line. As facilities rely more on high-tech equipment, this method of measurement has also become increasingly crucial.
While Industry 4.0 provides the means to improve machine performance monitoring, it also increases the need for it. Industry 4.0 has made the plastics industry a faster, more flexible and less wasteful sector, increasing market expectations. As the major players in the plastics industry become faster and more resilient, they are setting a new standard that others must meet.
Industry 4.0 requires compounders to deliver better performance to meet rising demand. At the same time, this trend is giving them the tools they need to pursue those goals. With these factors in mind, here we outline some ways manufacturers can improve their Industry 4.0 OEE.
1. Continuous in-line & real-time operational monitoring and sorting
The days of only manual periodic off-line sample checking are fading. Newly developed measurement methods, such as Inspec.Tech’s ‘smart’ in-line & real-time pellet inspection system, allows for continuous monitoring.
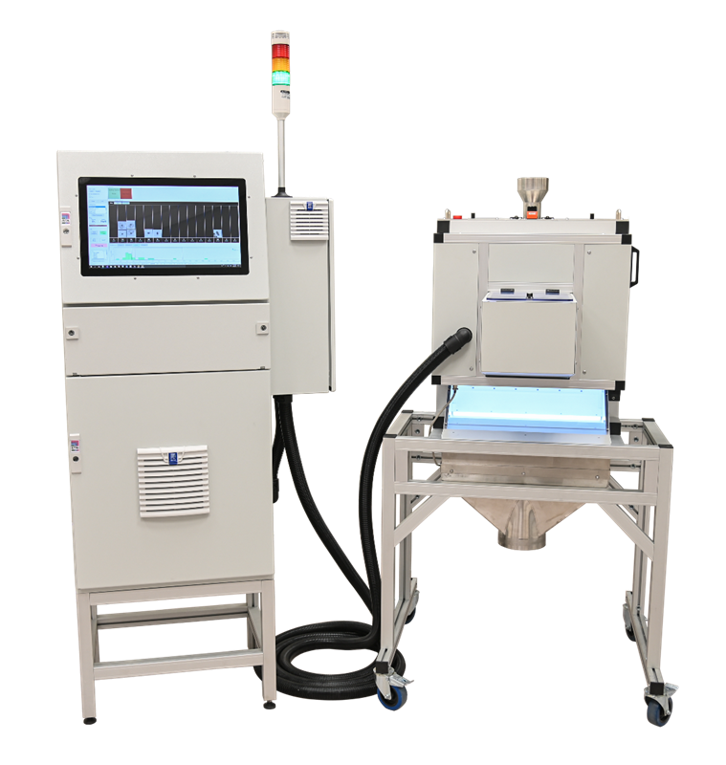
By integrating the ‘smart’ pellet inspection system into the extrusion line, compounders can continuous monitor the operational performance of an extrusion line in real-time. These cameras in combination with the underlying intelligence, monitor the pellets after the pelletizer and classifier and detect factors, such as black specks and other impurities, contour and size of pellets, detection of ‘tails’ and color variation, all simultaneously.

In the past, operators had to interrupt their operations for periodic monitoring to either visually check some of these factors or have them checked off-line, but with the deployment of Inspec.Tech’s ‘smart’ pellet inspection system, this is now done automatically, continuously and in real-time with data capture without disrupting production.
This data improves OEE by providing easy, accessible and real-time insight into the underlying aspects of an extrusion line’s performance. Because compounders can access this data in realtime, they get to the root cause of the problem faster. They can then address the problem and improve extrusion line performance sooner, leading to faster OEE improvements. Compounders can even use the ‘smart’ inspection system to provide real-time alerts and sorting off-spec pellets,
allowing them to improve line performance before an entire product rejection occurs.
2. Targeted notifications
Inspec.Tech’s ‘smart’ in-line & real-time pellet inspection system, can further improve OEE by providing more targeted insights and alerts. In addition to providing a continuous stream of data, the system can offer more specific data. With more specific data, compounders can address any issues more effectively, enabling deeper OEE analysis and improvements.
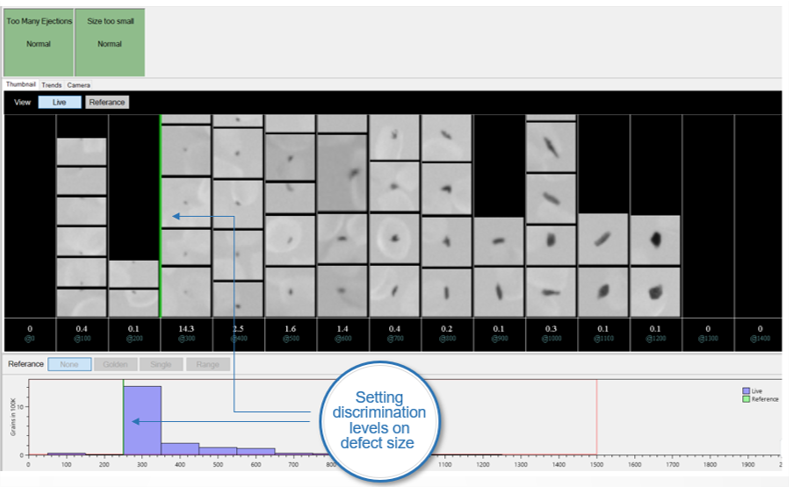
For example, during production the system can generate warnings for too large shift in particle size; for too large quantity of impurities; warnings for too large quantity of tails, for too large quantity of too small particles and warnings for too large colorshift.
The warnings are given on the basis of self-adjustable limit values and are all automatically normalized according to the measured production throughput in real time.
Also, during production, the system can generate alarms for too many times per unit of time that these warnings are given and automatically sort off-spec product.
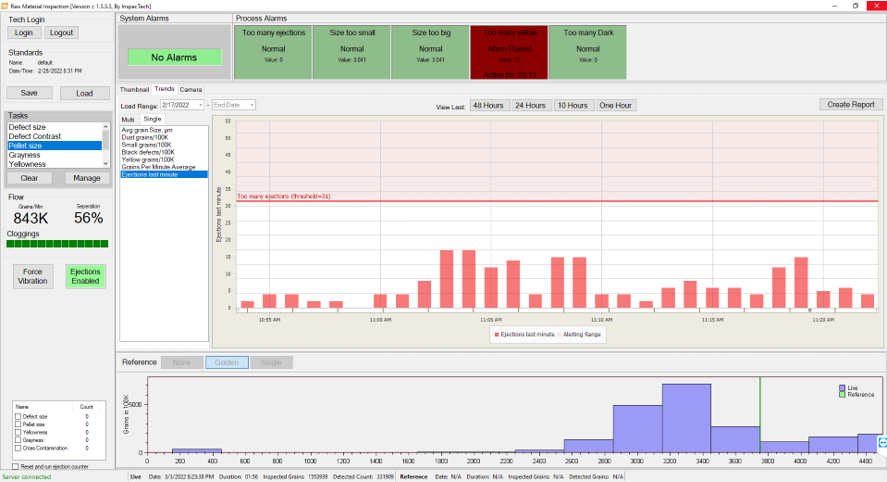
In addition, during production, Inspec.Tech’s ‘smart’ in-line & real-time pellet inspection system can provide insight into real-time actual performance compared to a so-called ‘golden reference’, a previous product run that serves as a benchmark. The histograms of real-time live production and ‘golden reference’ are superimposed and shown on the display.
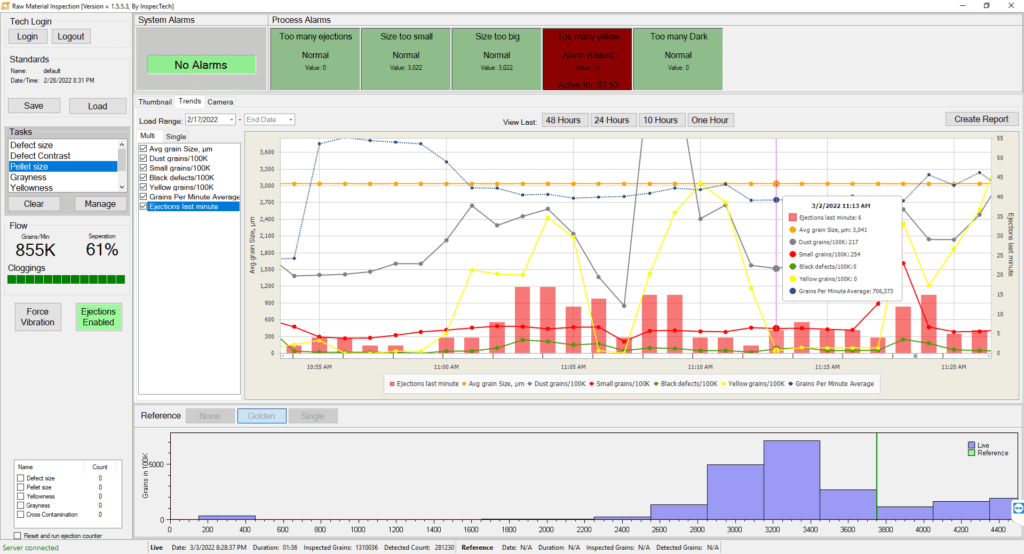
Continuous data collection and analysis will also reveal which changes led to the most significant OEE improvements. These insights allow compounders to improve their OEE calculations and future initiatives. Compounders can embrace a spirit of continuous improvement by focusing on these small, ongoing changes.
3. Data-driven predictive maintenance
Traditionally, most manufacturing companies either perform preventive maintenance on a schedule or reactive maintenance after an emergency. The ‘smart’ inspection system helps compounders apply predictive maintenance
Predictive maintenance uses big data or AI-driven analytics modules to analyze historical and current operational data. Inspec.Tech’s ‘smart’ in-line & real-time pellet inspection system makes operational data available through the cameras combined with the underlying intelligence. With this information, analysis engines can then predict when a machine will need maintenance or break
down. Compounders can then schedule a time to fix the problem before it becomes a more urgent issue.
This approach minimizes unplanned downtime that would result from reactive maintenance because failures are prevented. Improved uptime also translates into higher OEE, because it increases the availability score of an extrusion line.
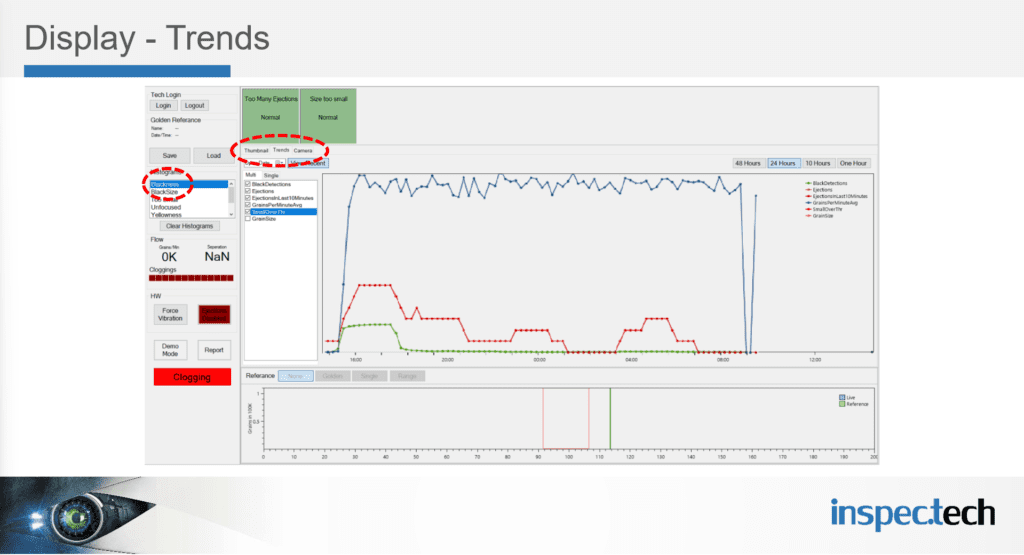
Deployment of the ‘smart’ inspection system also reduces the costs associated with schedulebased preventive maintenance. While these maintenance strategies also prevent failures, they can lead to unnecessary downtime and costs due to unnecessary repairs. Inspec.Tech’s ‘smart’ in-line & real-time pellet inspection system makes the various operational data available on which predictive maintenance is partly based rather than on schedules, so that only the necessary repairs are recommended maximizing uptime.
These strategies also improve OEE by minimizing machine-related quality problems. Predictive maintenance would fix these machine problems before they affect quality, eliminating waste.
No Industry 4.0 without OEE
Industry 4.0 is inextricably linked to OEE data. The need for OEE indicators is necessary to produce efficiently and flexibly, and conversely, Industrie 4.0 provides the necessary data and messaging to optimize OEE. Industry 4.0 is thus a neverending story of large and small optimizations and upgrades. In other words… the rat race for the smartest factories only just started.
Sources
Industrialfairs (www.industrialfairs.com)
Kunststof Magazine (www.kunststof-magazine.nl)
Inspec.Tech (www.inspec.tech)
OEE (www.oee.com)
Product portfolio of Inspec.Tech
As a knowledge specialist and representative in the BeNeLux, SPS | Solids Process Solutions would like to inform you about the inspection options for the quality of your pellets