Automatic approach to quality pellets
Globally, compounders are looking to automate their granulation process to improve quality,
efficiency, flexibility and safety and address a shortage of skilled personnel.
Today’s plastics industry, including compounders and recyclers who produce pellets, is responding
to a new business environment characterized by the challenges of fluctuations in the economy,
worker availability and material supply. Current supply chain issues complicate production planning
and lead to an increasing need for flexibility in operations, which must be supported by both
personnel and machinery.
Faced with such challenges, compounders must consider a comprehensive overall view of
downstream equipment, focusing on systems that are easily switched, cleaned, accessible and
flexible.
In-line & Real-time Pellet Inspection
With real-time visibility into the production process, efficient and appropriate action can be taken
when deviations are found that damage the intended quality of the pellets but also cause delays
and downtime; which is not desirable in today’s market situation. With Inspec.Tech’s In-line & Realtime pellet inspection, any problems are quickly identified. Think of contamination, change in size and shape or color shift.
In-line & Real-time versus Off-line inspection
The traditional way of inspecting, taking samples for testing in the laboratory, no longer suits today’s needs in production environments and also gives a distorted picture because it does not represent the complete production flow; as a result, problems could be missed. So by bringing the inspection into the production line now, adjustments can be made immediately with warnings of any problems. This presents opportunities for many granulator lines in a variety of environments, such as in the compounding and recycling industries, where this is not yet deployed.
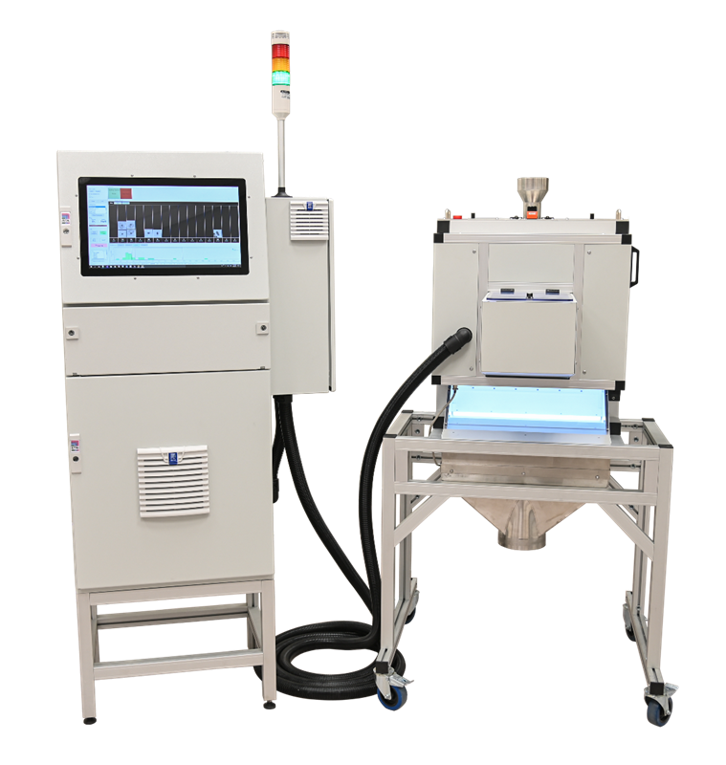
Variation in Recycling
The In-line & Real-time inspection system is also useful for the granulation process of recycling,
which is more susceptible to contamination. A major limitation in the use of recycled material is the quality of the product and the variability of the quality; In-line & Real-time inspection systems can
help reduce the quality variation.
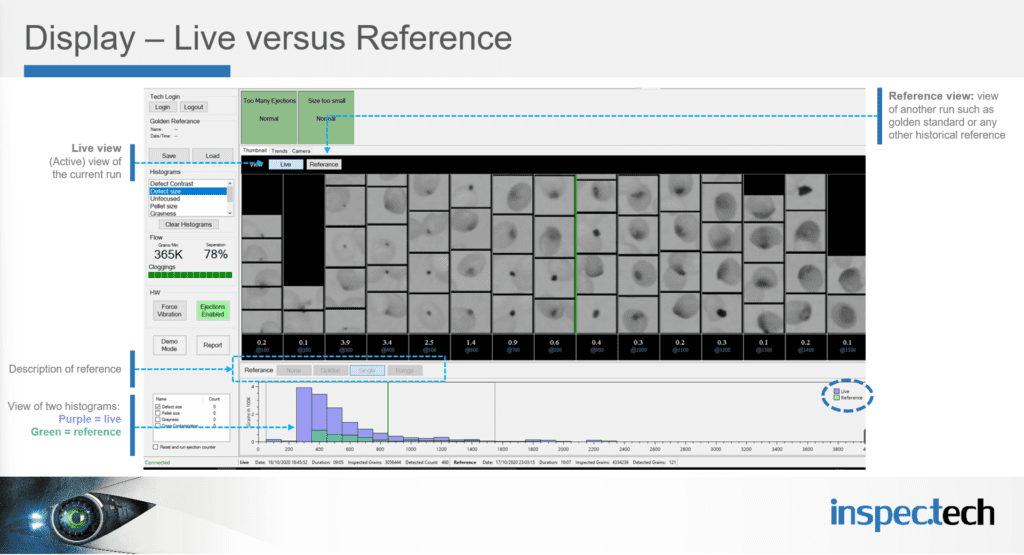
Inspec.Tech’s In-line & Real-time system is designed to withstand the harsh conditions in plastics production such as high temperatures, dust from flowing agents, abrasive or corrosive materials such as glass-filled masterbatches and crosslinking agents. Inspection Technologies offers three sizes of systems with throughputs from 1 to 9 tons/hour depending on system and application.
Method of operation
Instead of line scan cameras, Inspec.Tech uses surface cameras. Instead of a line of pixels, these contain a matrix of pixels allowing different exposures to be used in different parts of the image
frame. You can have multiple inspection tasks in one frame with different types of lighting in the upper and lower parts. For example, for dimensions you need to see good contours, so you need high contrast with the background. For impurities, such as detecting black specks, the system will use a different type of illumination.
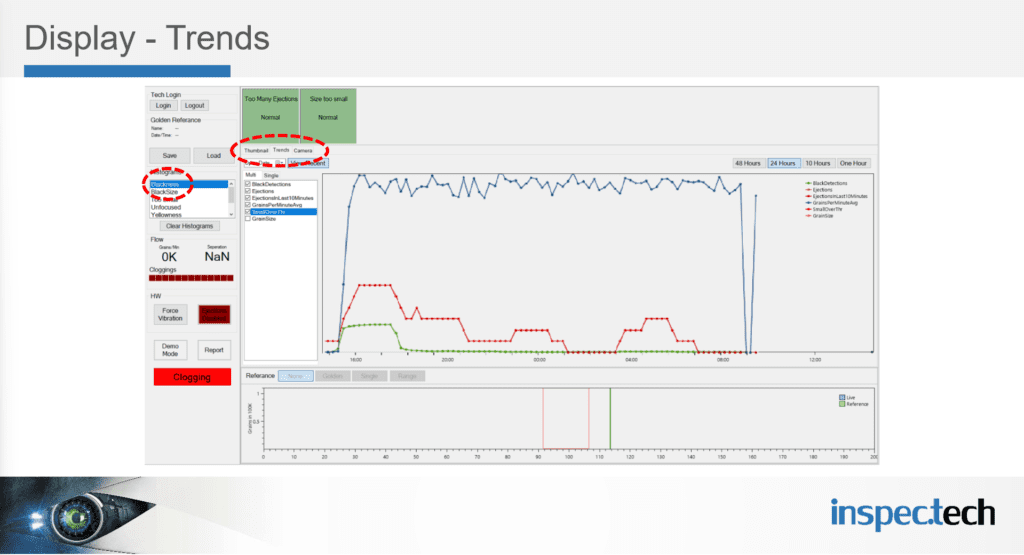
In addition to detecting impurities, the system also analyzes the pellet size and shape to detect improper cutting, such as “tails. The system shows the distribution of size and shape, and it indicates if that distribution is changing. You can immediately see if you are starting to get angel hair or tails, and you can set up a real-time alert if a control limit is exceeded. When inspection tasks involving pellet color are needed, color cameras can be added to the system.
Modular sorting unit for quality monitoring and efficiency
In addition to In-line & Real-time continuous monitoring, a sorting unit can be added to sort out poor quality pellets. The application of both monitoring and off-line sorting can be used to better plan and carry out maintenance. You don’t have to perform preventive maintenance at predetermined times, but you can do it as and when the monitoring gives you a signal that there is a problem.
View the solutions from Inspec.Tech
As a knowledge specialist and representative in the BeNeLux, SPS | Solids Process Solutions would like to inform you about the inspection options for the quality of your pellets